Drug Product Manufacturing
Drug product manufacturing is more than filling containers. We design, characterize, and validate the sterile product manufacturing process. We manufacture clinical and commercial sterile drug products according to cGMP using the most modern Isolator technology. At ten23 health we can perform aseptic drug product manufacturing. Our focus is on delivering safe and high-quality sterile drug products, enabling convenient application for patients.
Sterile drug product manufacturing (also known as fill&finish) consists of multiple operations, ranging typically from thawing and pooling drug substances in suitable storage containers, to compounding, microbial pre-filtration/sterile filtration, filling into clean, sterile, and depyrogenated (ready-to-use or RTU) containers (e.g. vials, syringes), possibly lyophilization (freeze-drying), and then closure and capping. Finally, all filled and closed containers have to undergo a 100% visual inspection and acceptable quality level (AQL) testing, as per GMP and pharmacopeial requirements. This process is also known as fill & finish in pharmaceutical manufacturing.
In sterile pharmaceutical manufacturing, sterility and absence of contaminants such as particulates are the key elements to define a sterile drug product. Sterility is preferably ensured by a process called terminal sterilization, where the final product is subjected to a sterilizing procedure, such as heat, to achieve sterility. For biologics, this is not doable because the terminal sterilization method would destroy the active ingredient, and hence, such products required to be produced aseptically, using sterile filtration.
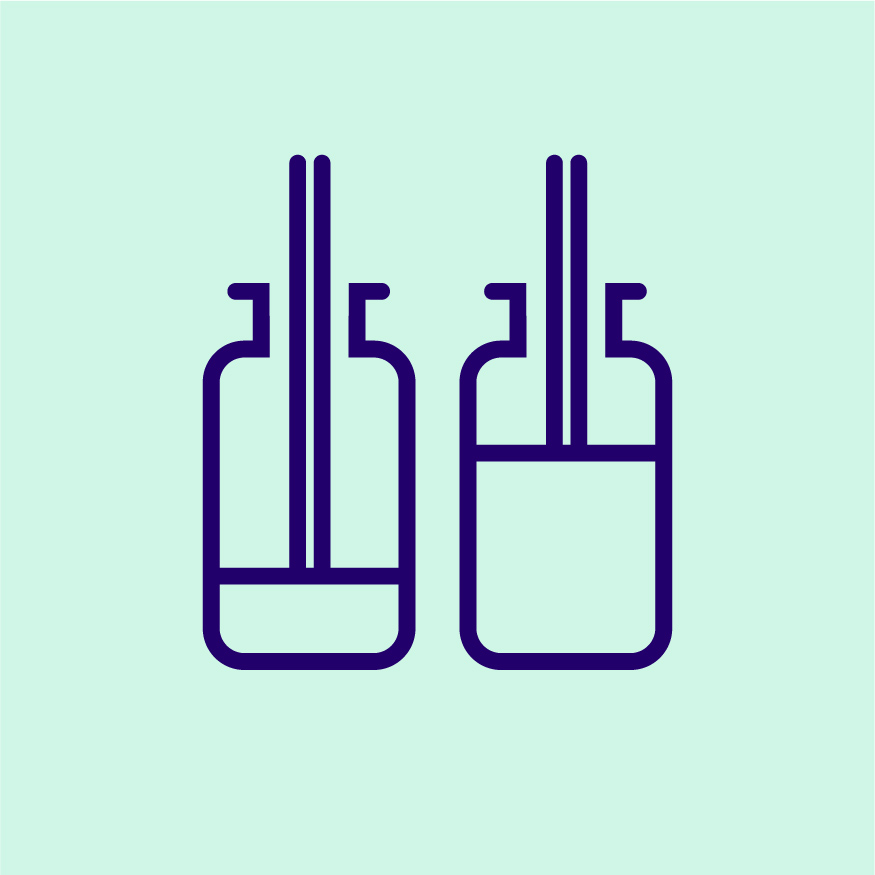
Manufacturing Process Transfer, Characterization and Validation
The manufacturing process needs to be diligently understood, considering the liabilities of the active ingredients and formulation as well as the manufacturing process performance in fill-finish. This also includes evaluating all unit operations for criticality, and considering and establishing process ranges, in relation to the critical quality attributes (CQA) of the product.
- moreless
Our experts at ten23 health support clients in designing an appropriate and robust manufacturing process for sterile fill-finish manufacturing. This includes material and supplier selection, as well as in-depth assessments and experiments related to individual process unit operations, and assessing product CQAs as a function of the chosen parameters. As an example, we can develop and improve lyophilization processes, as well as support filter selection, scale-up, and closure/capping.
The same diligence will be employed to transfer your process smoothly into our facility, as well as for successful validation of your process for commercial supply.
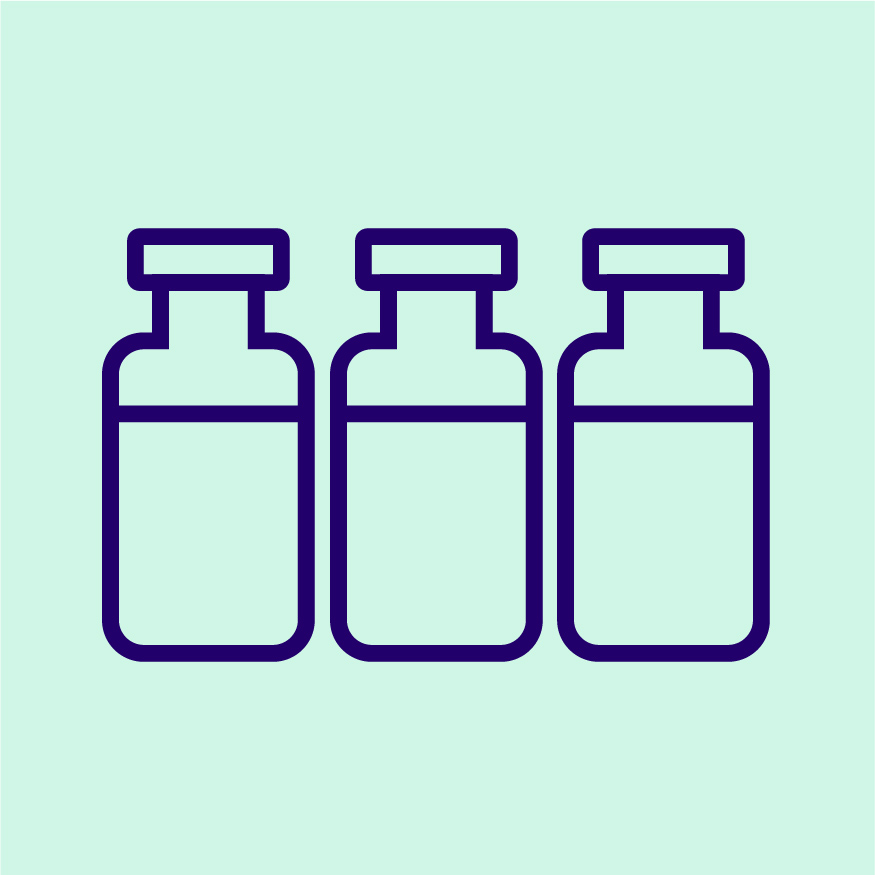
Stability Samples, Reference Standards & Pre-clinical Supplies manufacture
At ten23 health in Basel, we support you in manufacturing representative samples for regulatory stability purposes (IND, IMPD, BLA, MAA), verifying drug product shelf-life settings, as well as serving as technical or engineering runs for later GMP fills. We can also fill Reference Standards for analytical purposes.
Additionally, we provide the pharmaceutical products necessary for pre-clinical studies, such as GLP-controlled toxicological studies, as well as reference products required for quality control and testing purposes. We can fill various containers (vials, syringes, cartridges) in varying scales, and provide liquid dosage forms or lyophilizates in vials.
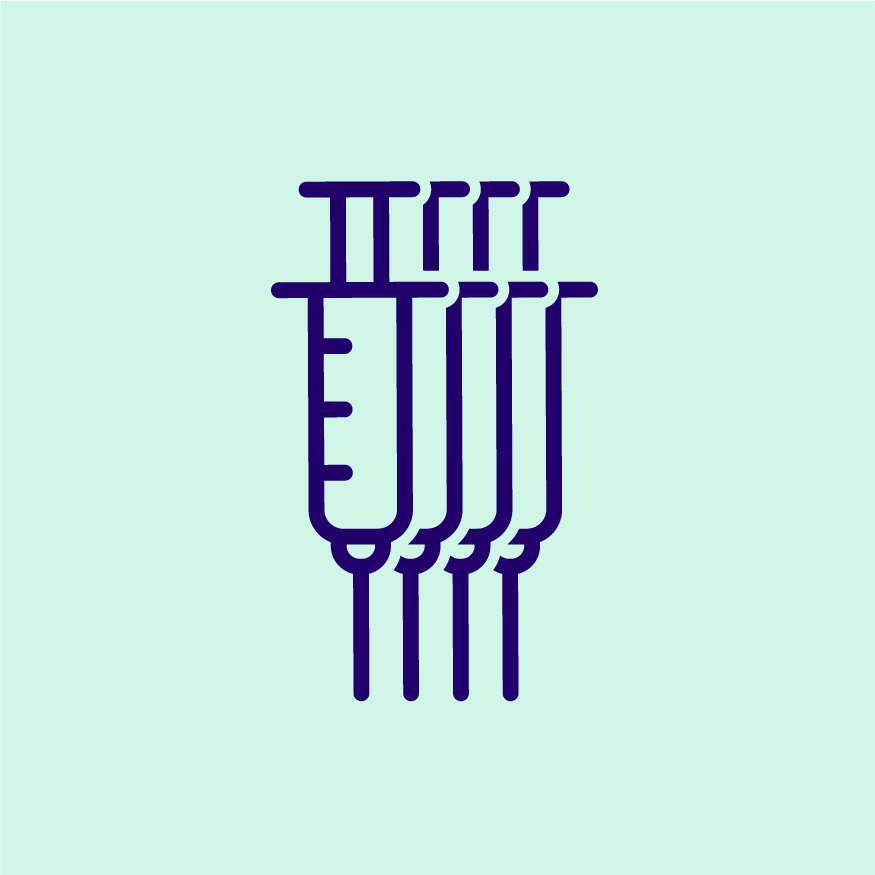
Clinical and Commercial Fill & Finish
Our Swissmedic- and FDA-inspected and GMP-approved sterile manufacturing site (“Line 1”) in Visp, Switzerland (VIVA1) is equipped with an Isolator line for vials, syringes, cartridges, and special devices. Batches can range from 1 Liter to 200 Liter bulk volume with minimal line losses and our typical batch size in units ranges from 500 to 20,000, depending on format and possible fill speed.
Batches of complex drug products, such as intravitreal preparations or subcutaneous formulations, are delivered with the highest quality and precision.
Additional capacity and capability for Sterile Manufacturing is being built by our Expansion with 2 more filling lines (VIVA2®).
Click here to find out more about our sites and filling lines.
- moreless
Our capabilities for sterile manufacturing on line 1 / VIVA1:
Clinical (phase 1 – 3) and Commercial (launch and initial supply) GMP manufacturing on the same line – saving time and material by avoiding costly transfers
Compounding volume 1 to 200 Liters, in glass bottles or plastic containers
Able to process a variety of Ready-to-use (RTU) containers, from vials (e.g., 2R to 30R) to syringes (e.g., 1 and 2.25 mL syringes), cartridges, and special containers for specific drug/device combination products, such as for the West SmartDose Device. All on the same filling line
Vials: courtesy of Stevanato Group
Syringe: courtesy of Terumo Europe
Cartridge and Smartdose: courtesy of West PharmaExperience with both glass and Polymer containers
Isolator based technology
Single or double sterile filtration with the option to perform PUPSIT (pre-use post sterilization integrity testing)
100% IPC testing for product weight (fill volume control)
Peristaltic or piston pump filling options
Super high-precision filling of small fill volumes such as 100 µL
No need for product-specific Cleaning Validation (dedicated and/or single-use materials)
Closed processing possible
Dedicated compounding room in class “C” environment
Open handling under laminar airflow (LAF) class “A”
Offline IPC testing, such as pH, osmolality, concentration, conductivity and density
100% visual inspection and AQL (acceptable quality level) testing
Our Expansion for sterile manufacturing (Line 2 and 3 / VIVA2)
read press release about the expansionLine 2
- Clinical and Commercial larger-scale GMP manufacture
- Same technology as Line 1, hence a direct and easy transfer to Line 2
- 8-headed filler
- Able to process a variety of Ready-to-use (RTU) containers, from vials (e.g., 2R to 30R) to syringes (e.g., 1 and 2.25 mL syringe), cartridges and special containers for specific drug/device combination products, such as for the West SmartDose Device.
- Experience with both glass and Polymer containers
- Isolator based technology
- Single or double sterile filtration with the option to perform PUPSIT (pre-use post sterilization integrity testing)
- 100% IPC testing for product weight (fill volume control)
- Peristaltic or piston pump filling options
Available for sterile filling from the end of 2024 onwards
Line 3
- Clinical (phase 1-3) and Commercial larger-scale GMP manufacture
- Bulk vial processing and Lyophilisation
- 2x 12.5 m2 Lyophilizers
- Able to process a variety of containers, from vials (e.g., 2R to 30R)
- Isolator based technology
- Single or double sterile filtration with the option to perform PUPSIT (pre-use post sterilization integrity testing)
- 100% IPC testing for product weight (fill volume control)
- Peristaltic or piston pump filling options
- Available for sterile filling from the end of 2025 onwards
Our strengths:- Clinical fills and commercial supplies out of one facility, without the need for lengthy and risky transfers
- Fill & finish services for complex drug products, such as intravitreal preparations or subcutaneously formulations
- Focus on maximum yield (minimum product losses)
- Highest filling accuracy
- 100% IPC for filled product weight
- Zero risk of cross-contamination
- Small volume filling (≤100µL), e.g., for intravitreal injection preparations
- Bubble-free filling
- Filling of highly viscous formulations
- Accurate stopper setting (+/- 0.5mm)
- Able to process Glass and COP/COC primary packaging
- Open to implement new formats and new generations of primary packaging